Соединения деталей с натягом - Лекция, раздел Образование, Классификация механизмов, узлов и деталей машин Это Условно Неразъемное Соединение, Т. К. Его Можно Разбирать Без Разр...
Это условно неразъемное соединение, т. к. его можно разбирать без разрушения, но повторная сборка-разборка снижает надежность.
Натяг образуется за счет положительной разности диаметра вала и отверстия во втулке (рисунок 9.18, а).
После сборки соединения диаметр d становится общим для вала и втулки. При этом на поверхности контакта развивается нормальное давление р (рисунок 9.18, б), которое является следствием упругих и упругопластических деформаций деталей соединения при сборке.. Как следствие давления в контакте также развивается сила трения, которая обеспечивает полную неподвижность соединения при действии внешних сил.
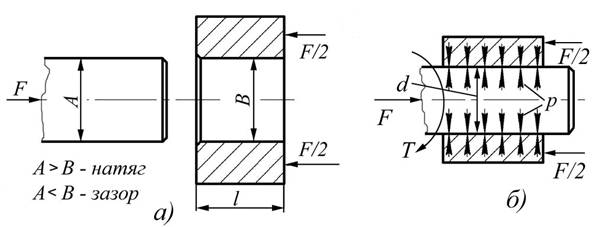
Рисунок 9.18 – Соединение с натягом: а) до запрессовки; б) после запрессовки
Сборка соединения с натягом может производиться: прессованием (запрессовкой); нагревом охватывающей детали; охлаждением охватываемой детали; гидрозапрессовкой.
Запрессовка – наиболее распространенный и несложный способ сборки. Основной недостаток – срез (смятие) неровностей поверхностей при запрессовке и уменьшение шероховатости поверхности, что снижает прочность соединения.
Нагрев охватывающей детали (до 230 ºС) распространенный способ. Недостаток – возможно коробление деталей, появление окалины и изменение структуры при более высокой температуре, поэтому рекомендуется нагревать детали в машинном масле.
Охлаждение охватываемой детали (до -79 ºС – углекислота и -196 ºС пары жидкого азота) очень выгодно применять для посадки малых деталей на большие (массивные) детали.
При гидрозапрессовке осуществляется нагнетание масла под давлением в зону контакта. Этот метод наиболее эффективен при сборке деталей больших диаметров и конических соединений. Недостаток – требует специального оборудования.
Области применения соединений: для посадки подшипников качения, ходовых колес, зубчатых колес, кулачков и т. п. на валы.
Преимущества:
1. Простота и технологичность, что обеспечивает низкую себестоимость и возможность применения в массовом производстве.
2. Хорошее центрирование (базирование) соединяемых деталей.
3. Возможность передачи больших знакопеременных нагрузок.
Недостатки:
1. Нагрузочная способность зависит от рассеивания значений коэффициента трения и колебаний действительных посадочных размеров.
2. Высокие сборочные напряжения.
3. Сложность сборки и особенно разборки при больших натягах
Целью расчета подобных соединений является определение величины требуемого натяга и выбора по нему стандартной посадки.
Значение этих параметров зависит от требуемого контактного давления р на посадочной поверхности. Это давление должно быть таким, чтобы сила трения на указанной поверхности, оказалась больше внешних сдвигающих сил и моментов. Определим величину этого давления, исходя из условия его равномерного распределения по контактной поверхности, для наиболее распространенных случаев (рисунок 9.18):
а) соединение нагружено осевой силой.
Условие отсутствия сдвига вала относительно втулки
| (9.57)
|
где К = 2 ÷ 4 – коэффициент запаса сцепления.
Сила трения в контакте
,
| (9.58)
|
где d – посадочный диаметр; f – коэффициент трения; l – длина посадочной поверхности.
Отсюда
,
| (9.59)
|
б) соединение нагружено крутящим моментом
Условие отсутствия сдвига деталей
,
| (9.60)
|
где момент трения
.
| (9.61)
|
Откуда
| (9.62)
|
в) соединение одновременно нагружено осевой силой и моментом (рисунок 9.18)
В этом случае векторы сдвигающей силы и крутящего момента взаимно перпендикулярны. Поэтому
| (9.63)
|
Откуда
| (9.64)
|
При сборке запрессовкой для стальных и чугунных деталей коэффициент трения f = 0,07, при температурной сборке f = 0,14. При сборке стальных и бронзовых деталей те же самые коэффициенты соответственно равны 0,05 и 0,07.
Используя известное решением задачи о напряжениях и деформациях в толстостенных полых цилиндрах (задача Ляме), приведенном в курсе сопротивления материалов, можно определить расчетный натяг
| (9.65)
|
где С1 и С2 – коэффициенты жесткости
и
| (9.66)
|
В этих уравнениях: d1 – диаметр отверстия охватываемой детали; d2 – наружный диаметр охватывающей детали (рисунок 9.19); Е1 и Е2, μ1 и μ2– модули упругости и коэффициенты Пуассона материалов вала и ступицы: для стали Е = 2,1∙105 МПа и μ = 0,3; для бронзы Е = 0,98∙105 МПа и μ = 0,35.
При сборке деталей запрессовкой микронеровности посадочных поверхностей частично срезаются и сглаживаются, что приводит к уменьшению натяга. Для учета влияния этого фактора вводят поправку u на обмятие микронеровностей
,
| (9.67)
|
где Ra1 и Ra2 – шероховатость посадочных поверхностей (3,2; 1,6; 0,8; 0,4 мкм и т. п.).
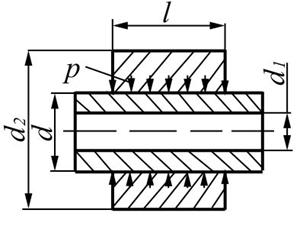
Рисунок 9.19 – Схема соединения с натягом
Для учета влияния температурного фактора вводят поправку на температурную деформацию
,
| (9.68)
|
где t1 и t2 – температура деталей соединения в процессе работы, 0С; α1 и α2 - температурные коэффициенты линейного расширения материала деталей (для стали α = 12∙10-6 0С-1).
При частоте вращения соединения больше 1000 мин-1 также необходима поправка для учета влияния центробежных сил
,
| (9.69)
|
где ρ – плотность материала втулки, (кг/м3); ω – угловая скорость, с-1.
С учетом влияния этих факторов действительный натяг находят по формуле
,
| (9.70)
|
По этому значению подбирают стандартную посадку, у которой минимальный натяг
| (9.71)
|
При этом рекомендуется выбирать предпочтительные посадки: H7/p6; H7/r6; H7/s6 и т. п.
На практике возможны случаи, когда выбранная посадка создает натяг, значительно превышающий допустимое значение. Это может привести к разрушению деталей соединения, в первую очередь – охватывающей детали (ступицы). Поэтому вал и ступицу необходимо проверить на прочность. Схема нагружения показана на рисунке 9.20.
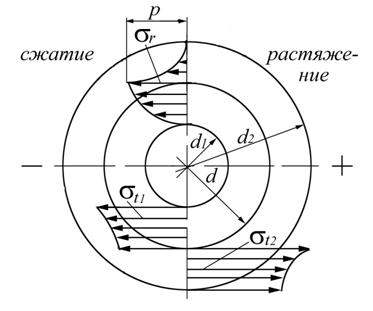
Рисунок 9.20 – Эпюры напряжений прессового соединения
Из курса сопротивления материалов известно, что для толстостенных сосудов наиболее опасными являются точки внутренней поверхности вала и втулки. В этих точках развиваются радиальные и тангенциальные напряжения.
Из рисунка 9.20 следует, что максимальное радиальное напряжение для вала и втулки
,
| (9.72)
|
максимальные тангенциальные напряжения для вала
,
| (9.73)
|
максимальное тангенциальное напряжение для втулки
,
| (9.74)
|
Т. к. вал и втулка одновременно подвергаются воздействию радиальных и тангенциальных напряжений, то по 3-й гипотезе условие прочности будет иметь вид:
для полого и сплошного вала
, ,
| (9.75)
|
где σТ1 – предел текучести материала вала.
Для втулки
,
| (9.76)
|
где σТ2 – предел текучести материала втулки.
Отсюда максимальное контактное напряжение для втулки
.
| (9.77)
|
что обеспечивает прочность соединения.
Вопросы к главе 9
1. Для чего предназначены, и какие виды соединений применяются в машиностроении?
2. Как происходит образование винтовой линии?
3. Назовите основные геометрические параметры резьбы?
4. Как различаются резьбы по назначению, геометрической форме и какие из них стандартизованы?
5. Какая резьба используется чаще – с мелким или крупным шагом и почему?
6. Что такое самоторможение, и от каких факторов зависит выполнение этого условия?
7. Какие ограничения по к.п.д. имеет винтовая пара?
8. Чем отличается расчет затянутых и незатянутых резьбовых соединений?
9. В чем преимущества и недостатки болтовых соединений, поставленных с зазором и без зазора и нагруженных поперечной силой?
10. Как влияет на диаметр болта тип уплотнительного элемента под крышкой сосуда, находящегося под давлением?
11. В чем преимущества и недостатки фрикционных клеммовых соединений?
12. Какие преимущества и недостатки шпоночных и шлицевых соединений?
13. Как подбираются по стандарту призматические и сегментные шпонки?
14. Как произвести проверочный расчет призматических и сегментных шпонок?
15. Какими достоинствами обладают шлицевые соединения по сравнению со шпоночными?
16. Какие существуют способы центрирования шлицевых прямобочных соединений?
17. По каким критериям работоспособности рассчитываются шлицевые соединения?
18. Какие преимущества и недостатки соединений с гарантированным натягом?
19. От чего зависит нагрузочная способность соединений с натягом, и какие факторы влияют на величину натяга?
20. Как подбирается стандартная посадка по расчетному натягу?
21. По какой причине может произойти разрушение соединения с натягом?
22. Какие виды сварки получили распространение в промышленности?
23. По каким признакам классифицируются сварные соединения и сварные швы?
24. В чем принципиальная разница в методике расчета сварных соединений, выполненных стыковыми и угловыми швами?
25. Какие факторы учитываются при определении допускаемых напряжений для сварных швов?
Введение к главе 10
Конструкция изделия должна максимально удовлетворять потребности пользователя, т. е. при низкой цене иметь высокое качество. Технические характеристики должны быть на уровне мировых достижений и иметь резерв развития. Это достижимо только при выполнении ряда важных требований к конструкции узлов и деталей машин:
- выбор наиболее рациональной схемы конструкции и ее элементов; создание изделий нового поколения;
- обеспечение показателей, заложенных в техническом задании и определяющих назначение, технические и экономические характеристики объекта: производительность, мощность, скорость движения, стоимость и т. д.;
- повышение надежности и ресурса, обусловленных свойствами изделия выполнять в течение заданного времени свои функции, сохраняя эксплуатационные показатели;
- уменьшение материалоемкости, что выполняется при создании компактной конструкции и изготовлении деталей из материала с высокой удельной прочностью;
- малое энергопотребление при эксплуатации, что реализуется при минимальных потерях на трене и высоком КПД;
- обоснованное назначение точности и шероховатости деталей и обеспечение их взаимозаменяемости;
- использование стандартизации и унификации деталей и их элементов;
- исключение попадания грязи, пыли и влаги на подвижные детали изделия путем использования уплотнений или защиты антикоррозионными покрытиями;
- использование элементов (лючков, регулировочных устройств и др.) для обеспечения технического обслуживания, ремонта и контроля;
- создание безопасности и комфорта оператору или исключение его присутствия;
- учет производственно-технологических требований.
Конструктивные решения, рассмотренные в этом разделе, основываются, в частности, на многолетнем опыте, обобщенном в капитальных трудах П. И. Орлова [5 Доп. лит.].
Все темы данного раздела:
Основные критерии работоспособности деталей машин
Работоспособность – это состояние изделия, при котором оно способно выполнять заданные функции с параметрами, установленными требованиями техдокументации.
Детали машин выходят из строя по
Объемная прочность
Основы расчета на объемную прочность подробно рассматриваются в курсе сопротивления материалов.
Рисун
Поверхностная прочность
Поверхностная прочность представляет особый класс задач, связанных с первоначальным контактом деталей в точке или по линии (подшипники качения, зубчатые, фрикционные передачи и т. д.). В этом случа
Жесткость
Жесткость – это способность деталей сопротивляться изменению формы и размеров под действием приложенной нагрузки.
Жесткость оценивают по величине силы, вызывающей единичное перемещение (ли
Износостойкость
Износостойкость – способность материала детали сопротивляться изнашиванию детали в определенных условиях трения (сухое, граничное, жидкостное) или иного воздействия (например, удар).
В про
Теплостойкость
Теплостойкость – это способность конструкции работать в пределах заданных температур в течение заданного срока службы.
Перегрев деталей машин может вызвать следующие вредные последствия:
Вибростойкость
Вибростойкостью называется способность конструкции работать в нужном диапазоне режимов, достаточно далеких от области резонанса.
Вибрация вызывает дополнительные переменные напряжения и, к
Кинематические и силовые соотношения в передачах
Каждая механическая передача состоит из двух звеньев – ведущего 1 и ведомого 2 (рисунок 2.3). Поэтому параметры, относящиеся к каждому звену, обозначаются соответственно индексами «1» и «2».
Основы теории зубчатого зацепления
В современном машиностроении в основном применяют эвольвентное зацепление, предложенное Эйлером в 1760 году. В 1954 г. М. Л. Новиковым было предложено принципиально новое зацепление, в котором проф
Выбор степени точности изготовления колес
Погрешности изготовления зубчатых колес приводит к повышению динамических нагрузок, вибрации, шуму передач. Основными погрешностями изготовления и монтажа зубчатых колес является погрешность окружн
Усилия в зацеплении зубчатых колес
В процессе работы передачи каждый зуб кратковременно входит в зацепление и выходит из него. При этом он находится в сложном напряженном состоянии, а также подвергается циклическому воздействию. Реш
Выбор материала для изготовления колес
При выборе материалов для зубчатых колес необходимо обеспечить прочность зубьев на изгиб, контактную прочность поверхностных слоев зубьев и сопротивление заеданию.
Основным материалом для
Виды разрушения зубьев
При передаче вращающего момента возникают упругие деформации профилей зубьев, вызывающие на поверхности зуба контактные напряжения σH, а у основания зуба напряжения изгиба σ
Расчет на контактную прочность
В прямозубых колесах зубья входят в зацепление сразу по всей длине. Это явление сопровождается ударами и шумом, особенно при высоких скоростях.
Расчет на контактную прочность выполняют, по
Расчет на изгибную выносливость
Наклонное расположение зубьев увеличивает их прочность на изгиб и уменьшает динамические нагрузки. Это учитывается введением поправочных коэффициентов в расчетную формулу для прямозубых передач (3.
Расчет на контактную прочность
Расчет зубьев прямозубых конических передач по контактным напряжениям проводим по той же методике, что и цилиндрических зубчатых передач. В основе расчета лежит формула Герца
Расчет на изгибную выносливость
Расчет на изгибную прочность конических прямозубых колес выполняют по зависимости, аналогичной прямозубой цилиндрической передаче (выражение 3.26):
Расчет червячных передач на контактную прочность
Червяки изготавливают из сталей типа 20Х, 18ХГТ с твердостью после цементации 57 ÷ 64 HRC, а также сталей типа 45, 40Х, 40ХН с поверхностной закалкой до твердости 45 ÷ 55 HRC. Во всех
Расчет червячных передач на изгибную выносливость
Расчет зубьев червячного колеса на изгиб проводим аналогично расчету косозубого зацепления. Только зубья червячного колеса из-за дугообразной (серповидной) формы примерно на 40 % прочнее цилиндриче
Тепловой расчет
Червячная передача работает с большим тепловыделением, что приводит к нагреву смазочного материала. Повышение температуры свыше 110 ˚С приводит к потере защитных свойств масляной плёнки и увел
А) передачи с трением скольжения
В грузовых механизмах применяют трапецеидальную и упорную резьбу. В ходовых механизмах чаще используют многозаходную трапецеидальную резьбу. В механизмах точных перемещений и установочных винтах пр
Б) передачи с трением качения
В передаче качения винтовые канавки служат дорожками качения для шариков. При вращении винта шарики увлекаются в направлении его поступательного движения, попадают в перепускной канал в гайке и воз
Планетарные зубчатые передачи
Планетарными называются передачи, имеющие зубчатые колеса с перемещающимися осями. Эти колеса называются сателлитами. Зубчатые колеса с общей центральной осью, с которыми взаимодейств
Волновые зубчатые передачи
Волновыми называются передачи, у которых передача вращательного движения осуществляется путем бегущей волны деформации одного из зубчатых колес.
Приводные ремни
Приводные ремни должны обладать достаточной прочностью, гибкостью, долговечностью, износостойкостью, высоким коэффициентом трения, низкой стоимостью. Наиболее распространены резинотканевые ремни и
Сравнительная оценка плоскоременной и клиноременной передачи
В современных приводах преимущественно используются клиноременные передачи, так как клиновидная форма поперечного сечения ремня позволяет существенно увеличить тяговую способность передачи.
Кинематика ременных передач
Упругое скольжение ремня характеризуется коэффициентом скольжения
,
(4.4
Геометрические параметры передачи
Диаметр ведущего шкива плоскоременной передачи определяют по формуле М. А. Северина
Усилия и напряжения в ремне
Для создания силы трения необходимо предварительное натяжение ремня силой F0 (рисунок 4.4, а). При этом ветви ремня удлинятся на величину λ.
Напряжения в ремне
При работе ременной передачи в поперечных сечениях ремня возникают следующие виды напряжений:
- напряжение от предварительного натяжения ремня
Критерии работоспособности и расчет ременной передачи
Основным критерием работоспособности ременных передач является тяговая способность – надежность сцепления ремня со шкивом и долговечность ремня, которая зависит в основном от сопротив
Расчет плоскоременных передач
Целью расчета по тяговой способности является определение площади поперечного сечения ремня по формуле
Расчет клиноременных передач
Так как клиновые ремни по площади поперечного сечения, а значит и по тяговой способности стандартизированы, то целью расчета является определение необходимого количества ремней
Критерии работоспособности и расчет ременной передачи
Основным критерием работоспособности ременных передач является тяговая способность – надежность сцепления ремня со шкивом и долговечность ремня, которая зависит в основном от сопротив
Расчет плоскоременных передач
Целью расчета по тяговой способности является определение площади поперечного сечения ремня по формуле
Расчет клиноременных передач
Так как клиновые ремни по площади поперечного сечения, а значит и по тяговой способности стандартизированы, то целью расчета является определение необходимого количества ремней
Приводные цепи
Основными типами приводных цепей являются роликовые, втулочные и зубчатые, параметры которых стандартизированы. Наиболее распространенными являются роликовые цепи (рисунок 5.2)
Основные параметры цепных передач
Передаточное число определяют из условия равенства окружных скоростей на обеих звездочках
Критерий работоспособности и расчет цепных передач
Цепные передачи выходят из строя чаще всего, по следующим причинам:
- износ шарниров, приводящий к удлинению цепи за счет увеличения шага и, как следствие, к нарушению зацепления цепи с зу
Расчетные нагрузки и методы расчета валов и осей
Основным критерием работоспособности валов и осей является прочность и жесткость.
На валы и оси при эксплуатации действуют нагрузки в виде сосредоточенных и распределенных си
Расчет валов и осей на жесткость.
Упругие деформации валов и осей, как правило, оказывают неблагоприятное влияние на работу подшипников, зубчатых зацеплений, шпоночных и шлицевых соединений и т. д. Поэтому при проектировании валов
Режимы работы подшипников
При конструировании подшипников скольжения всегда добиваются минимальных потерь на трение. Это приводит к экономии энергии, уменьшению тепловыделения и снижению износа сопряженных поверхност
Скольжения
На практике в подшипниках скольжения чаще всего реализуется смешанное трение. Однако для работы подшипников самым благоприятным является режим жидкостного трения.
Известны два способа созд
Нагрузочная способность и условный расчет подшипников скольжения.
Условный расчет позволяет предварительно оценить пригодность выбранного материала и размеров подшипника для конкретных условий работы на основании накопленного опыта конструирования и эксплуатации
Условные обозначения подшипников
Условное обозначение подшипников состоит из ряда цифр и букв, нанесенных на торце одного из колец:
- последние две цифры, умноженные на пять, обозначают внутренний диаметр d подшипника. Эт
Виды разрушений и критерий работоспособности подшипника
Основной причиной выхода из строя подшипников качения при нормальной эксплуатации и скоростях n ≥ 10 мин-1 является выкрашивание рабочих поверхностей колец и тел качения. Это связа
Расчетный ресурс подшипников качения.
Ресурс подшипников выражают в миллионах оборотов L или в часах Lh, которые связаны между собой соотношением:
Сварные соединения
Это наиболее рациональный и распространенный вид неразъемных соединений, приближающий по прочности составные детали к целым. Очень широко применяются в машиностроении.
Применяют следующие
Шпоночные соединения
Передача вращающего момента между деталями соединения осуществляется с помощью специальной детали – шпонки.
Шпонка – деталь в форме бруса (рисунок 9.4), устанавливаемая в пазах двух сопряг
Шлицевые (зубчатые) соединения
Шлицевое соединение условно можно рассматривать как многошпоночные, у которого шпонки (зубья) выполнены за одно целое с валом и входят в соответствующие пазы (шлицы), выполненные в ступице детали (
Резьбовые соединения
Резьбовыми называют соединения, выполненные при помощи резьбы. К ним относят соединения при помощи болтов (винт с гайкой), винтов, шпилек и т. д. Это одно из старейших и наиболее распространенных в
Момент завинчивания
Резьбовые соединения собирают путем завинчивания винтов или гаек. Затяжку резьбовых соединений осуществляют при помощи гаечных ключей.
Момент завинчивания Тзав, который с
Самоторможение винтовой пары
Опусканию ползуна по наклонной плоскости соответствует случай отвинчивания гайки (рисунок 9.9, б). В этом случае окружная сила Ft и сила трения меняют направление. Из указанной сх
К.п.д. винтовой пары
Этот показатель можно определить как отношение полезной работы к затраченной. Согласно схеме, показанной на рисунке 9.9, а, полезная работа заключается в вертикальном перемещении груза
Расчет резьбы на прочность
Практика показывает, что основными причинами разрушения резьбовых соединений являются:
1. Усталостное разрушение в виде обрыва стержня винта (более 65 % случаев).
2. Срез резьбы (
А) расчет незатянутого винтового соединения.
Этот случай характерен для крюковых подвесок кранов, рым-болтов и т. д. (рисунок 9.14).
Рисунок 9.14
Б) расчет затянутого винтового соединения.
Этот случай характерен для крепления крышек сосудов, находящихся под давлением, что требует обеспечения герметизации соединения.
В этом случае кроме растяжения тела винта усилием затяжки F
А) винт поставлен с зазором.
Рисунок 9.15 – Болтовое соединение, работающее на сдвиг (болт поставлен с зазором)
В этом случае внеш
Б) винт поставлен без зазора.
В этом случае затяжка отсутствует, винт поставлен в отверстие детали без зазора (легкой запрессовкой), поэтому отверстие обрабатывают под развертку.
Фрикционно-винтовые (клеммовые) соединения
Принцип действия клеммовых соединений основан на использовании сил трения, развивающихся между цилиндрическими поверхностями за счет затяжки винта.
Преимущества:
Проектирования
В настоящее время успешно развивается система автоматизированного проектирования (САПР).
Необходимо учитывать, что любое изделие, отвечающее своему назначению, может быть выполнено во мног
Способах изготовления
При конструировании новых изделий, необходимо учитывать не только факторы, обеспечивающие работоспособность (прочность, жесткость, износостойкость и т. д.) при минимальной материалоемкости и
Механически обрабатываемые детали
Сокращение объема механической обработки, может быть достигнуто путем максимального приближения размеров заготовки к окончательной форме детали. Например, при изготовлении шестигранных гаек,
Особенности конструирования литых изделий
В механизмах малой мощности (до 100 кВт) литые корпуса желательно изготовлять из алюминиевых и магниевых сплавов. Это позволяет снизить массу деталей почти в три раза по сравнению с чугунными издел
Новости и инфо для студентов