Превращения, протекающие в структуре стали при нагреве и охлаждении - раздел Образование, КОНСТРУКЦИОННЫХ МАТЕРИАЛОВ
В Результате Термической Обработки В Сплавах Происходят Струк...
В результате термической обработки в сплавах происходят структурные изменения. После термообработки металлические сплавы могут находиться в равновесном (стабильном) и неравновесном (метастабильном состоянии).
Равновесное состояние достигается тогда, когда полностью завершаются все протекающие в сплавах процессы. При этом строение сплава будет соответствовать диаграмме состояния. Неравновесное состояние получается при условиях, препятствующих полному завершению протекающих процессов (например, при наклепе).
Увеличение теплового движения атомов при нагреве способствует переходу в равновесное состояние.
В основе всех превращений, которые совершается в стали при нагреве, лежит стремление системы к минимуму свободной энергии (рис. 7.2).
Теоретически превращение перлита в аустенит должно совершаться при А1=727 oC. Фактически же для превращения нужен перегрев. Кроме этого, чем выше t oC, тем быстрее совершается превращение Fea«Feg, а также растворение цементита Fe3C в аустените.
Превращение начинается с зарождения центров аустенитных зерен на поверхности раздела – феррит-цементит. Аустенит обнаруживается уже при небольших нагревах - до температуры 727oC и очень малых выдержках.
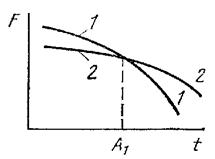
Рис. 7.2. Изменение свободной энергии аустенита (1) и перлита (2) в зависимости от температуры
При медленном охлаждении стали, происходит обратное превращение. Термодинамическим условием этого превращения является некоторая степень переохлаждения, когда свободная энергия перлита становится меньше свободной энергии аустенита. При охлаждении стали с большей скоростью, кинетику и механизм превращения аустенита выясняют с помощью постановки специальных экспериментов, на основании которых строят диаграмму изотермического превращения аустенита.
Рассмотрим кинетику и механизм превращения переохлажденного аустенита на примере стали эвтектоидного состава, содержащей 0,8% углерода. Нагретые до температуры на 30-50 oC выше критической точки, соответствующей превращению П→А (точка А1), образцы, имеющие структуру однородного аустенита, переносят в термостаты с заданной температурой. Наблюдают за изменениями магнитных характеристик образцов (аустенит парамагнитен, а феррит и цементит обладают магнитными свойствами), что позволяет оценить кинетику превращений аустенита в перлит при различных температурах.
Получают серию кинетических кривых (рис. 7.3), которые показывают количество образовавшегося перлита в зависимости от времени, прошедшего с начала превращения.
Вначале наблюдается инкубационный (подготовительный) период, время, в течение которого сохраняется переохлажденный аустенит. Превращение протекает с различной скоростью и достигает максимума при образовании 50 % продуктов распада. Точки Н1, Н2, Н3 соответствуют началу, точки К1, К2,К3 – концу превращения.
Затем скорость начинает уменьшаться и постепенно затухает. С увеличением степени переохлаждения устойчивость аустенита уменьшается, а затем увеличивается.
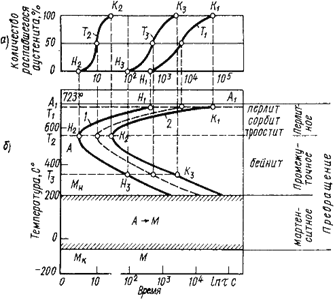
Рис. 7.3. Кинетические кривые превращения аустенита при охлаждении (а); диаграмма изотермического превращения аустенита (б)
Наибольшая скорость превращения П→А для эвтектоидной стали достигается при переохлаждении на 150-200 oC ниже точки А1(точка Н2 на графике). Начиная с этой температуры (Т2) дальнейшее ее снижение приводит к уменьшению скорости превращения.
Преобразуя координаты, по полученным опытным кривым проводят построение диаграммы изотермического превращения переохлажденного аустенита (рис. 7.3 б).
Диаграмма изотермического превращения аустенита для эвтектоидной стали представляет результат обобщения многочисленных данных исследований превращений аустенита при постоянных температурах (рис. 7.4.). За сходство этих кривых с буквой «с» их также называют С-диаграммами или ТТТ – диаграммами.
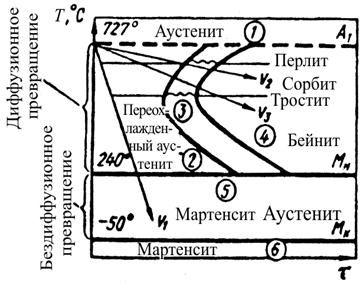
Рис. 7.4. Диаграмма изотермического превращения аустенита эвтектоидной стали
На диаграмме можно выделить следующие области:
(1) – область устойчивого аустенита
(2) – область переохлажденного аустенита
(3) – область начинающегося, но еще не закончившегося превращения А®П
(4) – область закончившегося превращения
(5) – область начинающегося, но еще не закончившегося мартенситного превращения (между Мн®Мк)
(6) - мартенситная область (ниже Мк)
Это кривая изотермического превращения эвтекооидной стали (0,8%С).
Для доэвтектоидных сталей на диаграмме изотермического превращения добавляется кривая выделения феррита из аустенита (рис. 7.5. а), а для заэвтектоидных сталей - кривая выделения цементита из аустенита (рис. 7.5. в).
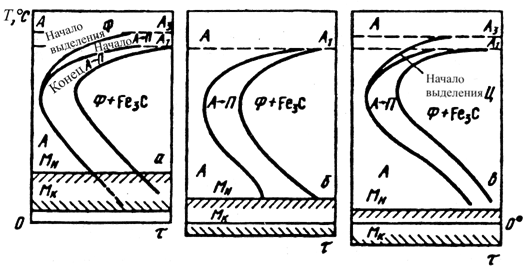
Рис. 7.5. Диаграмма изотермического превращения переохлажденного аустенита а) – доэвтектоидной стали; б) - эвтектоидной стали; в) - заэвтектоидной стали
Расстояние от оси ординат до линии начала превращения, характеризует меру устойчивости аустенита. Диаграмма изотермического превращения позволяет определить конечную структуру для конкретной марки стали, если известна температура или скорость превращения.
Перлит, сорбит, троостит является структурами одной природы – механической смесью феррита и цементита и отличаются друг от друга лишь степенью дисперсности. С увеличением степени дисперсности пластин цементита, то есть с понижением температуры распада, растет твердость и прочность стали. Под степенью дисперсности понимают расстояние между соседними пластинками феррита и цементита.
Наибольшую пластичность имеют стали с сорбитной структурой. Троостит характеризуется меньшей пластичностью.
При охлаждении ниже 500 оС до t начала мартенситного превращения образуется игольчатая структура бейнита (или игольчатого троостита). Бейнит отличается от перлитных структур более высоким содержанием углерода в феррите. Бейнитные участки имеют игольчатый характер.
При больших степенях переохлаждения возрастает термодинамическая неустойчивость аустенита, а скорость диффузии углерода резко падает. При переохлаждении аустенита в эвтекоидной стали до 240 оС подвижность атомов углерода близка к нулю, и происходит бездиффузионное превращение аустенита. При этом меняется лишь тип решетки a-g, а весь углерод, ранее растворенный в решетке аустенита, остается в решетке феррита. Образуется мартенсит Feα (C) - пересыщенный твердый раствор внедрения углерода в a - железе. Мартенсит имеет туже концентрацию углерода как и исходный аустенит.
Из-за пересыщенности углеродом решетка мартенсита искажена и имеет тетрагональную форму. Чем больше углерода, тем выше степень тетрагональности мартенсита.
Мартенсит имеет высокую твердость и хрупкость HRC=65. При переходе от аустенитной к мартенситной структуре объем и размеры детали увеличиваются.
7.3. Технологические возможности и особенности отжига, нормализации, закалки и отпуска
При разработке технологии необходимо установить:
· режим нагрева деталей (температуру и время нагрева);
· характер среды, где осуществляется нагрев и ее влияние на материал стали;
· условия охлаждения.
Режимы термической обработки назначают в соответствии с диаграммами состояния и диаграммой изотермического распада аустенита.
Нагрев может осуществляться в нагревательных печах, топливных или электрических, в соляных ваннах или в ваннах с расплавленным металлом, пропусканием через изделие электрического тока или в результате индукционного нагрева.
С точки зрения производительности, нагрев с максимальной скоростью уменьшает окалинообразование, обезуглероживание и рост аустенитного зерна. Однако необходимо учитывать перепад температур по сечению, что ведет к возникновению термических напряжений. Если растягивающие напряжения превысят предел прочности или предел текучести, то возможно коробление или образование трещин.
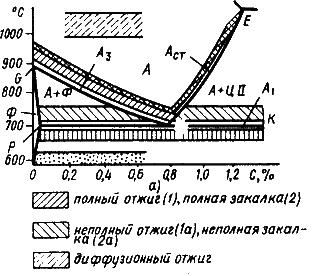
Рис. 7.6. Левый угол диаграммы состояния железо – цементит и температурные области нагрева при термической обработке сталей
Скорость нагрева тем выше, чем менее легирована сталь, однороднее ее структура, проще конфигурация.
Скорость нагрева принимается 0,8…1 мин на 1 мм сечения. Время выдержки принимается около 20 % от времени нагрева.
Среда нагрева при нагреве в печи с газовой средой. Составляющие могут оказывать на сталь различное действие: окисляющее (О2, СО2, Н2О);
восстанавливающее (СО, СН4); обезуглероживающее (О2, Н2); науглероживающее (СО, СН4); нейтральное (N2, инертные газы).
Окисление с образованием окалины Fe2O3, препятствует получению высокой и равномерной твердости при закалке, приводит к изменению размеров, требует увеличения припусков на механическую обработку.
Обезуглероживание (выгорание углерода в поверхностном слое металла) способствует появлению мягких пятен при закалке и возникновению растягивающих напряжений в поверхностном слое, снижающих усталостную прочность.
На рис. 7.6 показаны температурные области нагрева при термической обработке сталей.
Отжиг и нормализация
Отжиг, снижая твердость и повышая пластичность и вязкость за счет получения равновесной мелкозернистой структуры, позволяет:
-улучшить обрабатываемость заготовок давлением и резанием;
-исправить структуру сварных швов, перегретой при обработке давлением и литье стали;
-подготовить структуру к последующей термической обработке.
Характерно медленное охлаждение со скоростью 30…100oС/ч.
Отжиг первого рода
1.Диффузионный (гомогенизирующий) отжиг. Применяется для устранения ликвации, выравнивания химического состава сплава.
В его основе – диффузия. В результате нагрева выравнивается состав, растворяются избыточные карбиды. Применяется, в основном, для легированных сталей.
Температура нагрева зависит от температуры плавления, ТН = 0,8 Тпл.
Продолжительность выдержки: τ = 8…20 часов.
2.Рекристаллизационный отжиг проводится для снятия напряжений после холодной пластической деформации.
Температура нагрева связана с температурой плавления: ТН = 0,4 Тпл.
Продолжительность зависит от габаритов изделия.
3.Отжиг для снятия напряжений после горячей обработки (литья, сварки, обработки резанием, когда требуется высокая точность размеров).
Температура нагрева выбирается в зависимости от назначения, находится в широком диапазоне: ТН = 160……700oС.
Продолжительность зависит от габаритов изделия.
Детали прецизионных станков (ходовые винты, высоконагруженные зубчатые колеса, червяки) отжигают после основной механической обработки при температуре 570…600oС в течение 2…3 часов, а после окончательной механической обработки, для снятия шлифовочных напряжений – при температуре 160…180oС в течение 2…2,5 часов.
Отжиг второго рода предназначен для изменения фазового состава.
Температура нагрева и время выдержки обеспечивают нужные структурные превращения. Скорость охлаждения должна быть такой, чтобы успели произойти обратные диффузионные фазовые превращения.
Является подготовительной операцией, которой подвергают отливки, поковки, прокат. Отжиг снижает твердость и прочность, улучшает обрабатываемость резанием средне- и высокоуглеродистых сталей. Измельчая зерно, снижая внутренние напряжения и уменьшая структурную неоднородность способствует повышению пластичности и вязкости.
В зависимости от температуры нагрева различают отжиг:
1.полный, с температурой нагрева на 30…50 oС выше критической температуры А3.
Проводится для доэвтектоидных сталей для исправления структуры.
При такой температуре нагрева аустенит получается мелкозернистый, и после охлаждения сталь имеет также мелкозернистую структуру.
2.неполный, с температурой нагрева на 30…50oС выше критической температуры А1.
Применяется для заэвтектоидных сталей. При таком нагреве в структуре сохраняется цементит вторичный, в результате отжига цементит приобретает сферическую форму (сфероидизация). Получению зернистого цементита способствует предшествующая отжигу горячая пластическая деформация, при которой дробится цементитная сетка.Структура с зернистым цементитом лучше обрабатываются и имеют лучшую структуру после закалки. Неполный отжиг является обязательным для инструментальных сталей.
Иногда неполный отжиг применяют для доэвтектоидных сталей, если не требуется исправление структуры (сталь мелкозернистая), а необходимо только понизить твердость для улучшения обрабатываемости резанием.
3.циклический или маятниковый отжиг применяют, если после проведения неполного отжига цементит остается пластинчатым. В этом случае после нагрева выше температуры А1 следует охлаждение до 680 oС, затем снова нагрев до температуры 750…760) oС и охлаждение. В результате получают зернистый цементит.
4.изотермический отжиг – после нагрева до требуемой температуры, изделие быстро охлаждают до температуры на 50…100oС ниже критической температуры А1 и выдерживают до полного превращения аустенита в перлит, затем охлаждают на спокойном воздухе. Температура изотермической выдержки близка к температуре минимальной устойчивости аустенита.
В результате получают более однородную структуру, так как превращение происходит при одинаковой степени переохлаждения. Значительно сокращается длительность процесса. Применяют для легированных сталей.
5.Нормализация. – разновидность отжига.
Термическая обработка, при которой изделие нагревают до аустенитного состояния, на 30…50 oС выше А3 или Аст с последующим охлаждением на воздухе.
В результате нормализации получают более тонкое строение эвтектоида (тонкий перлит или сорбит), уменьшаются внутренние напряжения, устраняются пороки, полученные в процессе предшествующей обработки. Твердость и прочность несколько выше чем после отжига.
В заэвтектоидных сталях нормализация устраняет грубую сетку вторичного цементита.
Нормализацию чаще применяют как промежуточную операцию, улучшающую структуру. Иногда проводят как окончательную обработку, например, при изготовлении сортового проката.
Для низкоуглеродистых сталей нормализацию применяют вместо отжига.
Для среднеуглеродистых сталей нормализацию или нормализацию с высоким отпуском применяют вместо закалки с высоким отпуском. В этом случае механические свойства несколько ниже, но изделие подвергается меньшей деформации, исключаются трещины.
Все темы данного раздела:
Ю.Г. Баскин, В.Ф. Глазков, Л.А. Королева, М.Н. Федотов
Материаловедение. Технология конструкционных материалов: учебное пособие /Под ред. В.С. Артамонова. – СПб.: Санкт-Петербургский университет Государственной противопожарной службы МЧС России, 2011 -
Характерные свойства металлов
В огромном ряду материалов, с незапамятных времен известных человеку и широко используемых им в своей жизни и деятельности, металлы всегда занимали особое место.
Подтверждение этому и в на
Понятие об изотропии и анизотропии
Свойства тела зависят от природы атомов, из которых оно состоит, и от силы взаимодействия между этими атомами. Силы взаимодействия между атомами в значительной степени определяются расстояниями меж
Прочность металлов идеального и реальных строений. Виды дефектов кристаллической решетки
Из жидкого расплава можно вырастить монокристалл. Их обычно используют в лабораториях для изучения свойств того или иного вещества.
Металлы и сплавы, полученные в обычных у
Макро и микроанализ
Различают макроструктуру, микроструктуру и тонкую структуру материалов.
1.Макроструктурный анализ – изучение строения металлов и сплавов невооруженным глазом или при
Термодинамические основы, механизм и кинетика кристаллизации металлов
Состояние вещества связано с условиями, в которых оно находится. Одно и тоже вещество в различных интервалах температур и давлений может находиться в состояниях, отличающихся друг от друга по своим
Параметры кристаллизации
Размер зерна металла сильно влияет на его механические свойства. Эти свойства, особенно вязкость и пластичность, выше, если металл имеет мелкое зерно.
Стремятся к получению
Механические свойства металлов и сплавов
Основными механическими свойствами являются прочность, упругость, вязкость, твердость. Зная механические свойства, конструктор обоснованно выбирает соответствующий материал, обеспечивающий надежнос
Напряжения и деформация
Деформацией называется изменение формы и размеров тела под действием напряжений.
Напряжение – сила, действующая на единицу площади сечения детали.
Напряжения и вызыв
Возвратная рекристаллизация структуры металла
Деформированный металл находится в неравновесном состоянии. Переход к равновесному состоянию связан с уменьшением искажений в кристаллической решетке, снятием напряжений, что опреде
Понятия о сплавах и их теория
Под сплавом понимают вещество, полученное сплавлением двух или более элементов. Возможны другие способы приготовления сплавов: спекания, электролиз, возгонка. В этом случае вещества
Термодинамические условия равновесия в двухкомпонентных сплавах
Различают следующие виды диаграмм состояния двухкомпонентных сплавов:
1.Диаграмма состояния сплавов с неограниченной растворимостью компонентов в твердом состоянии (сплавы
Влияние углерода и примесей на свойства стали.
Стали являются наиболее распространенными материалами. Обладают хорошими технологическими свойствами. Изделия получают в результате обработки давлением и резанием.
Достоинс
Виды термической обработки металлов
Свойства сплава зависят от его структуры. Основным способом, позволяющим изменять структуру, а, следовательно, и свойства является термическая обработка.
Основы термической
Закалка
Основными параметрами являются температура нагрева и скорость охлаждения.
По температуре нагрева различают виды закалки:
– полная, с температурой нагрева на 30…50
Обработка стали холодом
Высокоуглеродистые и многие легированные стали имеют температуру конца мартенситного превращения (Мк) ниже 0oС. Поэтому в структуре стали после закалки наблюдается знач
Поверхностная закалка стали, виды и область применения
Конструкционная прочность часто зависит от состояния материала в поверхностных слоях детали. Одним из способов поверхностного упрочнения стальных деталей является поверхностная з
Химико-термическая обработка стали
Химико-термическая обработка (ХТО) – процесс изменения химического состава, микроструктуры и свойств поверхностного слоя детали.
Изменение химического состава поверх
Термомеханическая обработка стали
Одним из технологических процессов упрочняющей обработки является термомеханическая обработка (ТМО).
Термомеханическая обработка относится к комбинированным способам
Методы поверхностного упрочнения
Основное назначение методов механического упрочнения поверхности – повышение усталостной прочности.
Методы механического упрочнения – наклепывание поверхностного слоя на глубину 0,2…0,4 мм
Конструкционные стали
Конструкционные материалы предназначены для изготовления деталей машин, конструкций и сооружений.
К конструкционным сталям, применяемым для изготовления разнообразных деталей машин, предъя
Углеродистые стали
Низкоуглеродистые стали 05 кп, 08, 10, 10 пс обладают малой прочностью высокой пластичностью. Применяются без термической обработки для изготовления малонагруженных деталей – шайб, прокладок
Цементуемые и улучшаемые стали
Используются для изготовления деталей, работающих на износ и подвергающихся действию переменных и ударных нагрузок. Детали должны сочетать высокую поверхностную прочность, твердость и достаточную в
Стали для режущего инструмента
Инструментальная сталь должна обладать высокой твердостью, износостойкостью, достаточной прочностью и вязкостью (для инструментов ударного действия).
Режущие кромки могут нагреваться до те
Высокопрочные стали
Высокопрочными называют стали, имеющие предел прочности более 1500 МПа, который достигается подбором химического состава и оптимальной термической обработки.
Такой уровень прочности можно
Коррозионно-стойкие стали и сплавы
Разрушение металла под воздействием окружающей среды называют коррозией.
Коррозия помимо уничтожения металла отрицательно влияет на эксплуатационные характеристики деталей, содейств
Жаростойкие и жаропрочные стали и сплавы
Жаростойкость, жаростойкие стали и сплавы
Жаростойкость (окалиностойкость) – это способность металлов и сплавов сопротивляться газовой коррозии при высоких температу
Магнитные стали и сплавы
Магнитотвердые стали и сплавы применяют для изготовления постоянных магнитов. Для постоянных магнитов применяют высокоуглеродистые стали с 1% C, легированные хромом (3%) EX3, а также одновременно х
Алюминий и его сплавы
Алюминий – легкий металл с плотностью 2,7 г/см3 и температурой плавления 660oС. Имеет гранецентрированную кубическую решетку. Обладает высокой тепло- и электропроводностью. Хи
Деформируемые магниевые сплавы
Магний плохо деформируется при нормальной температуре. Пластичность сплавов значительно увеличивается при горячей обработке давлением (360…520oС). Деформируемые сплавы маркируют МА1, МА8
Пресс-порошки и пресс-материалы
Пресс-порошками называются композиционные пластмассы с порошкообразным органическим и неорганическим наполнителем (древесная мука, целлюлоза, кварцевая мука, микроасбест и др.).
Высоконаполненные конструкционные пластмассы
К таким пластмассам относятся материалы, у которых доля наполнителя доходит до 70-75% от массы. В таких высоконаполненных материалах армирующий наполнитель вводится в виде листов, тканей, непрерывн
Газонаполненные пластмассы
Газонаполненные пластмассы это легкие и сверхлегкие материалы, которые получают вспениванием эмульсии и раствора полимера воздухом или газом, либо газами, выделяющимися в процессе отверждения полим
Резиновые материалы
Резинами называются высокомолекулярные материалы, которые получают при вулканизации смеси натурального или синтетического каучука с различными налолнителями. В состав резиновой смеси входят следующ
Клеящиеся материалы и герметики
Клеи и герметики относятся к пленкообразующим материалам и имеют много общего с ними. Эти растворы или расплавы полимеров, а также неорганические вещества, которые наносятся на какую-либо поверхнос
Электротехнические материалы
Электротехнические материалы представляют собой совокупность проводниковых. электроизоляционных, магнитных и полупроводниковых материалов, предназначенных для работы в электрическ
Проводниковые материалы
К этой группе материалов относятся металлы и их сплавы. Чистые металлы имеют малое удельное сопротивление. В качестве проводниковых материалов применяют медь, алюминий, редко - серебро. Исключение
Электроизоляционные материалы
Электроизоляционными материалами, или диэлектриками, называют такие материалы, с помощью которых осуществляют изоляцию, т. е. препятствуют утечке электрического тока между какими-либо токопроводя
Магнитные материалы
В зависимости от назначения различают магнитно-твердые и магнитно-мягкие материалы.
Магнитно-твердые материалы применяют для изготовления постоянных магнитов. Они должны иметь высокие знач
Полупроводниковые материалы и изделия
К полупроводниковым материалам относится большое количество материалов, отличающихся друг от друга внутренней структурой, химическим составом и электрическими свойствами. Согласно химическому сос
Требования, предъявляемые материалам
Автомобильные детали изготавливаются из углеродистых, легированных, специальных сталей, чугунов различной структуры, цветных сплавов, отливаемых на различной основе. Соответственно
Причины отказов
Изменение технического состояния автомобилей, агрегатов и механизмов происходит под влиянием постоянно действующих причин, обусловленных работой самих механизмов, случайных: причин,
Виды изнашивания деталей
1)Механическое изнашивание происходит в результате механических воздействий. Оно имеет четыре подвида.
Абразивное изнашивание проявляется вследствие попадания между трущимися поверхностями
Общая характеристика способов повышения надежности
Потребительский уровень каждого изделия, в том числе и автомобиля, оценивается его качеством, под которым, как правило, понимается надежность. Надежность работы машин в эксплуатации зависит от ряда
Мероприятия по повышению надежности конструкции
Основные конструктивные мероприятия, направленные на повышение надежности машин, могут быть сведены в такие группы:
1.Упрощение конструктивной схемы машины, уменьшение числа составляющих э
Технологические мероприятия повышения надежности
Расчетный уровень надежности, заложенный в машину на стадии проектирования в конструкторском бюро, должен быть обеспечен в процессе изготовления деталей и элементов, сборки и регулировки машин. Вст
Материалы, применяемые в машиностроении
Железо и его сплавы, т. е. стали и чугуны, бесспорно, являются основными техническими материалами, которые используются в машиностроении. Второе место среди конструкционных материал
Технологические методы получения заготовок
При производстве автомобилей используется литье, обработка давлением, прокат, спекание, комбинированные методы получения заготовок.
Различают литье в разовые и многоразовые формы. Р
Металлургическое производство и его продукция
Современное металлургическое производство представляет собой комплекс различных производств, базирующихся на месторождениях руд и коксующихся углей, энергетических комплексах. Оно в
Производство чугуна
Чугун – сплав железа и углерода с сопутствующими элементами (содержание углерода более 2,14 %).
Исходными материалами для производства чугуна являются: железная руда; флюсы
Продукты доменной плавки
Передельный чугун предназначается для дальнейшего передела в сталь. На его долю приходится 90 % общего производства чугуна. Обычно такой чугун содержит 3,8…4,4 % углерода, 0,3…1,2 % кремния, 0,2…1
Важнейшие технико-экономические показатели работы доменных печей
1.Коэффициент использования полезного объёма доменной печи (КИПО) – это отношение полезного объема печи V (м3) к ее среднесуточной производительности Р (т)
Производство стали в кислородных конвертерах
Кислородно-конвертерный процесс – выплавка стали из жидкого чугуна в конвертере с основной футеровкой и продувкой кислородом через водоохлаждаемую фурму. В настоящее время способ яв
Производство алюминия
Технология процесса производства алюминия состоит из трех этапов:
1.Извлечение глинозема из алюминиевых руд (бокситов)
2.Электролиз расплавленного глинозема с получение первичного
Общие положения
Современное машиностроение широко использует детали из порошковых материалов.
Порошковая металлургия - область техники, охватывающая совокупность методов и
Методы получения порошков и их подготовка
Типовая технологическая схема получения изделий методами порошковой металлургии включает:
-производство порошков;
-формование заготовки из порошка;
-спекание заготовки;
Основные свойства порошков
Механические порошки характеризуются технологическими и физическими свойствами, а так же химическим составом.
К технологическим свойствам порошков относятся: насыпной вес, текучесть и прес
Способы производства изделий из металлических порошков
Одним из главных этапов производства изделий из металлических порошков после их получения является формование заготовок. Формование – это придание порошковому материалу формы, размеров, плотности и
Напыление металлов
В последние годы для нанесения на детали защитных и упрочняющих покрытий, а также для восстановления изношенных поверхностей широкое применение нашло применение различных способов напыления. Все он
Требования к материалам, используемым для получения отливок
Для литья в различной степени пригодны все металлы и их сплавы. Однако чтобы качество отливок удовлетворяло техническим требованиям, сплавы, из которых изготовляются отливки, должны (удовлетворять)
Особенности конструкции и технологичности отливок
При выборе способа литья для получения заготовки в первую очередь должен быть рассмотрен вопрос экономии металла. Металлоемкость можно снизить конструктивными и технологическими мероприятиями. Част
Формообразование машиностроительных профилей
18.2. 1. Прокатное производство
Прокатка – это наиболее распространенный способ обработки пластическим деформированием. Прокатке подвергают до 90 % в
Продукция прокатного производства
Форма поперечного сечения называется профилем проката. Совокупность профилей различной формы и размеров - сортамент.
В зависимости от профиля прокат делится на четыре основные группы: лист
Прессование
Прессование – вид обработки давлением, при котором металл выдавливается из замкнутой полости через отверстие в матрице, соответствующее сечению прессуемого профиля.
Волочение
Сущность процесса волочения заключается в протягивании заготовок через сужающееся отверстие (фильеру) в инструменте, называемом волокой. Конфигурация отверстия определяет форму полу
Оборудование для ковки
В качестве оборудования применяются ковочные молоты и ковочные прессы.
Оборудование выбирают в зависимости от режима ковки данного металла или сплава, массы поковки и ее конфигурации. Необ
Холодная объемная штамповка
Холодная штамповка производится в штампах без нагрева заготовок и сопровождается деформационным упрочнением металла.
Холодная штамповка является одним из наиболее прогресси
Листовая штамповка
Листовая штамповка – один из видов холодной обработки давлением, при котором листовой материал деформируется в холодном или подогретом состоянии.
Листовой штамповкой
Композиционные материалы с нуль-мерными наполнителями
В композиционных материалах этого типа наибольшее распространение получила металлическая матрица из металла или сплава. Композиции на металлической основе упрочняются равномерно распределенными дис
Композиционные материалы с одномерными наполнителями
В композиционных материалах этого типа упрочнителями являются одномерные элементы в форме нитевидных кристаллов, волокон (проволоки). Волокна и другие армирующие элементы скрепляютс
Эвтектические композиционные материалы
Эвтектическими композиционными материалами называют сплавы эвтектического или близкого к эвтектическому состава, в которых упрочняющей фазой выступают ориентированные кристаллы, образующиеся в проц
Изготовление деталей из полимерных композиционных материалов
В качестве матрицы в композиционных материалах на неметаллической основе используют отвержденные эпоксидные, полиэфирные, фенолополиамидные и другие смолы. Наиболее распространены композиции, армир
Обработка и соединение композиционных материалов
На практике часто возникает необходимость соединения деталей узлов из композиционных материалов между собой и с конструкциями, выполненными из металлов и сплавов. В этом случае задача сводится к об
Нанокристаллические материалы
Нанокристаллическими называют материалы с размерами кристаллов (зерен или частиц) менее 100 нм. По комплексу свойств они существенно отличаются от обычных материалов такого же химического
Технология изготовления резиновых изделий и область их применения
Технология приготовления резиновых смесей состоит из ряда операций, выполняемых в определенной последовательности. Основные операции — подготовка ингредиентов, их смешивание и получ
Влияние условий эксплуатации на свойства резин
Пространственно-сетчатая структура вулканизированных резин определяет многие их свойства. Резинам свойственна большая обратимая деформация, достигающая 100%, при сравнительно низких напряжениях. Ст
Физико-химические основы сварки
Сварка – технологический процесс получения неразъемных соединений материалов посредством установления межатомных связей между свариваемыми частями при их местном или общем на
Основные способы сварки и их особенности
В настоящее время известно более 70 способов сварки, отличающихся разнообразием технологических процессов. Это связано как с применением разных способов нагрева деталей (электрической дугой, газоки
Дуговая сварка
Несмотря на успех в разработке новых способов сварки, доминирующее положение занимает дуговая сварка, которая занимает до 60 % всего объема сварочных работ).
Источником те
Электрошлаковая сварка
Сущность процесса заключается в том, что тепловую энергию, необходимую для расплавления основного и присадочного металла, дает теплота, выделяемая в объеме шлаковой ванны при прохождении через нее
Лучевые способы сварки
Электронно-лучевая сварка.
Сущность процесса состоит в том, что свариваемые детали, собранные без зазора, помещают в вакуумную камеру и подают на них электродный луч – пучок электро
Газовая сварка
При газовой сварке заготовки 1 и присадочный материал 2 в виде прутка или проволоки расплавляют высокотемпературным пламенем 4 газовой горелки 3 (рис. 20.4).
Ультразвуковая сварка
Ультразвуковая сварка относится к процессам, в которых используют давление, нагрев и взаимное трение свариваемых поверхностей. Силы трения возникают в результате действия на заготовки, сжатые осево
Сварка взрывом
Большинство технологических схем сварки взрывом основано на использовании направленного взрыва.
Соединяемые поверхности заготовок, одна из которых неподвижна и служит основанием, располага
Сварка трением
Сварка трением–способ сварки давлением при воздействии теплоты, возникающей при трении свариваемых поверхностей.
Свариваемые заготовки устанавливают соосно в зажима
Контактная сварка
Контактная сварка относится к видам сварки с кратковременным нагревом места соединения без оплавления или с оплавлением и осадкой разогретых заготовок. Характерная особенность этих процессов – плас
Диффузионная сварка
Диффузионная сварка–способ сварки давлением в вакууме приложением сдавливающих сил при повышенной температуре.
Свариваемые детали тщательно зачищают, сжимают, нагре
Специальные термические процессы в сварочном производстве
Наплавка – процесс нанесения слоя металла или сплава на поверхность изделия.
Наплавка позволяет получать детали с поверхностью, отличающейся от основного металла, на
Термическая резка металлов
Газокислородная резка заключается в сжигании металла в струе кислорода и удалении этой струей образующихся оксидов. При горении железа в кислороде выделяется значительное количество теплоты
Пайка металлов
Пайкой называют процесс соединения деталей посредством припоя – сплава, который смачивает поверхности деталей и, затвердевая, связывает их. Припой прочно соединяется с поверхностью изделия только т
Способы пайки по удалению оксидной пленки
Флюсовая пайка. Для обеспечения удаления оксидов с поверхности паяемых металлов и припоя, а также для предупреждения образования новых оксидов при нагреве в процессе пайки применяются паяльн
Способы пайки по кристаллизации паяного шва
Кристаллизация при охлаждении. Как правило, температура нагрева при пайке на 50—100° выше температуры плавления припоя. При этой температуре вследствие взаимодействия основного металла и при
Способы пайки по заполнению зазора
Капиллярная пайка. Пайка, при которой расплавленный припой заполняет паяльный зазор и удерживается в нем преимущественно поверхностным натяжением, называется капиллярной. Капиллярные явления
Способы пайки по источнику нагрева
Пайка в печи. Ее применение в производстве объясняется следующими факторами.
1.Высокой производительностью.
2.Высокой стабильностью качества паяного соединения.
3.
Способы пайки по получению припоя
Пайка готовым полностью расплавляемым припоем. Пайка, при которой используется заранее изготовленный припой, называется пайкой готовым припоем.
Пайка композиционным припоем.
Технологический процесс пайки
Технологический процесс пайки включает комплекс выполняемых операций, основными из которых являются следующие: подготовка поверхностей под пайку; сборка деталей; укладка припоя, в ряде случаев нане
Склеивание деталей
Склеиванием называют соединение деталей тонким слоем быстротвердеющего раствора – клея. Процесс склеивания состоит из подготовки соединяемых поверхностей деталей, нанесения к
Дефекты сварных и паяных соединений
При производстве сварных и паяных конструкций могут возникать дефекты, т. е. отдельные несоответствия продукции нормативным требованиям. Влияние дефекта на работоспособность конструкции зависит не
Методы контроля качества сварных и паяных соединений
Методы контроля бывают двух типов: разрушающие и неразрушающие.
К разрушающим относятся испытания сварных образцов-свидетелей. Сваривают их при тех же самых режимах, что и изделия, обычно
Заклепочные и прессовые соединения
Заклепочные соединения выполняют с помощью специальных крепежных деталей – заклепок (рис. 20.7 а, б) или непосредственным расклепыванием цапф деталей (рис. 20.7 в, г).
Заклепка пред
Формирование качества поверхности технологическими методами
Обеспечение требуемой шероховатости поверхности. Обыкновенно поперечная шероховатость больше продольной (вдоль действия инструмента, в частности резца) и поэтому, когда говорят
Металлорежущие станки
Обработка ведется на металлорежущих станках, обеспечивающих: необходимое усилие резания; регулируемое относительное перемещение инструмента и детали в пространстве с требуемой скоростью, позволяюще
Точение
Точение является основным способом обработки поверхностей тел вращения.
Ри
Сверление
Сверление является основным способом получения глухих и сквозных цилиндрических отверстий в сплошном материале заготовки.
В качестве инструмента при сверлении используется сверло, имеющее
Протягивание
Протягивание является высокопроизводительным методом обработки деталей разнообразных форм, обеспечивающим высокую точность формы и размеров обрабатываемой поверхности. Применяется протягивание в кр
Фрезерование
Фрезерование – высокопроизводительный и распространенный метод обработки поверхностей заготовок: многолезвийным режущим инструментом – фрезой (рис. 22. в).
Главным движением при фрезерован
Строгание
Обработка строганием характеризуется прямолинейным возвратно-поступательным главным движением и прерывистым движением подачи. Главное возвратно-поступательное движение состоит из двойных ходов. Во
Шлифование
Шлифование – процесс обработки заготовок резанием с помощью инструментов (кругов), состоящих из абразивного материала (рис. 22.1 е,ж).
Абразивные зерна расположены беспорядочно. При
Хонингование
Применяют для получения отверстий высокой точности, малой шероховатости и высокой степени цилиндричности, а также для создания на стенках специфического микропрофиля, способствующего лучшему удержа
Суперфиниширование
Является окончательным методом тонкой обработки, в процессе которого получается особо гладкая поверхность. При этом значительно снижается высота микронеровностей.
Поверхности обрабатывают
Полирование
Полированием уменьшают шероховатость поверхности.
Этим способом получают зеркальный блеск на ответственных частях деталей (дорожки качения подшипников) либо на декоративных элемента
Притирка
Притиркой (доводкой) обрабатываются плоские, осесимметричные и фасонные поверхности. Этот метод позволяет достигнуть наивысшей степени точности и наименьшей шероховатости поверхности. Процесс осуще
Ультразвуковая обработка
Позволяет обрабатывать не только токопроводные материалы, как сказано выше, но и токонепроводящие материалы в том числе хрупкие и твердые, например, алмаз, азотированные стали, полупроводники (крем
Выбор способов обработки
Каждая деталь может быть представлена в виде сочетания таких элементарных поверхностей, как: плоскости. Цилиндры, конусы, торы и пр. Более сложные поверхности: винтовые, шлицевые, зубчатые и другие
ЗАКЛЮЧЕНИЕ
Металлы относятся к числу наиболее распространенных материалов, которые человек использует для обеспечения своих жизненных потребностей. В настоящее время всё большее применение нах
Новости и инфо для студентов